Actions for responsible purchasing
- Commitment #9 -
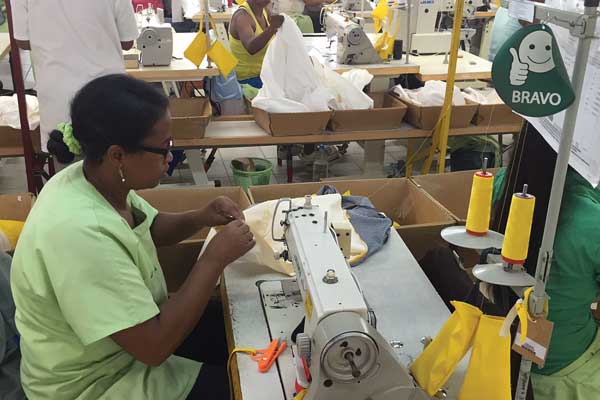
Focus 2023
CEPOVETT, hand in hand with its workshops
CEPOVETT has forged close links between its design offices based in France and its technical teams abroad.
This close working relationship with the Group's factories has enabled us to reduce product development times, thus improving our profitability and efficiency. To ensure optimum quality for all its customers, CEPOVETT has set up a laboratory where tests can be carried out to verify the conformity and performance of textiles to the most demanding standards. This in-house expertise enables all CEPOVETT group brands to increase their responsiveness when it comes to industrializing their PPE products, and to guarantee the best possible performance. EPSILON's workshops in Madagascar and VTL's in Tunisia guarantee product industrialization under the best technical and economic conditions.
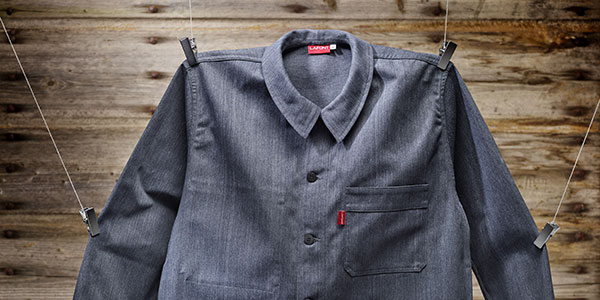
Focus 2022
Regenerated fiber, the material of the future
As part of its recycling program initiated in 2015, CEPOVETT has made the reclamation of end-of-life business attire a key focus.
To give these garments a second life, the company uses innovative materials to obtain a 100% circular fabric, made from "post-consumer" recycled polyester and cotton fabrics. This is the case, for example, with medical gowns which, when mixed with recycled polyester, produce a 100% regenerated fiber after reprocessing. The materials extracted from post-consumer garments are shredded and blended with this fiber, which is composed of one-third recycled cotton, one-third recycled polyester from textiles and one-third recycled polyester from plastic bottles. Thanks to this innovative solution, CEPOVETT is able to recycle end-of-life garments, saving virgin materials and natural resources used by the textile industry.
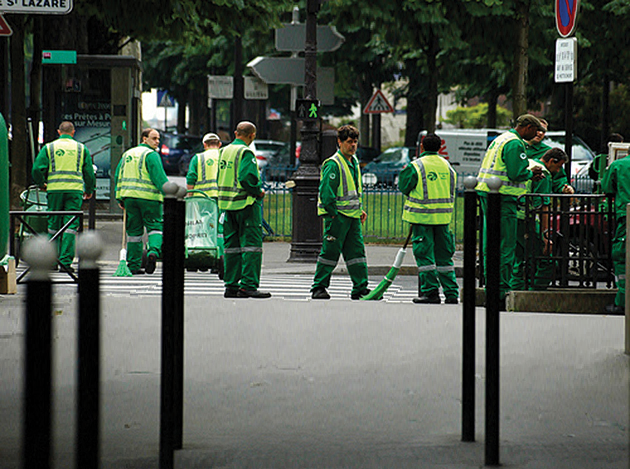
Focus 2021
Recycled materials mandatory in public procurement
Published in the Journal Officiel on March 9, 2021, Decree No. 2021-254 on the obligation to acquire through public procurement goods from reuse or reutilization or incorporating recycled materials comes to implement the provisions of Article 58 of Law No. 2020-105 of February 10, 2020 on the fight against waste and the circular economy, which entered into force on January 1, 2021.
The decree obliges public authorities to increase the proportion of circular-economy purchases, and reinforces the principle that public procurement should take into account the environmental performance of products. As a result, the proportion of recycled materials sourced from reuse or recycling channels must represent at least 20% of all textile products ordered by local authorities and semi-public companies. CEPOVETT has been proposing several solutions in this direction for several years, including recycled polyester from recycled plastic bottles and post-consumer recycled cotton. These new regulations reinforce the French government's policy of responsible purchasing.
Focus 2020
Secure sourcing
The recent Covid-19 epidemic was a wake-up call for textile manufacturers, penalized by their essentially Asian sourcing. This health crisis underlines the need to diversify supply channels, giving priority to sources closer to home, in particular the Maghreb and Madagascar. To achieve this, purchasing teams are rebalancing and securing their supplier portfolios, while integrating CSR aspects. CEPOVETT relies on a "CEPOVETT FabLab" support program for its suppliers, based on a collaborative approach with its garment workshops. Through a multi-year 360° CSR action plan, the program aims to bring out a number of best practices in technical, economic, social and societal innovation. The company is also committed to guaranteeing the transparency of its production sites and the security of its supplies through SMETA-type social and environmental audits.
Focus 2019
ISO 14001 certification of the Epsilon CEPOVETT Group workshop
ISO 14001 is the most widely used international standard for environmental management. It is based on the principle of continuous improvement of environmental performance by controlling and measuring the impact of a company's activities. ISO 14001 is the name of an environmental management standard whose features are designed to reassure even the most demanding, environmentally conscious customers. Over the long term, Epsilon's environmental management system will be enriched by new tools for dialogue and cost control, but above all for mobilizing employees.
Focus 2018
CEPOVETT Group Fablab", a lever for innovation in France and abroad
CEPOVETT Group relies on an ambitious program to support its suppliers. The "CEPOVETT Group FabLab" program is based on a voluntary and collaborative approach with its garment workshops in its main production zones around the world (Eastern Europe, Asia and North Africa). Through experimentation and a multi-year 360° CSR action plan, the program aims to develop best practices in technical, economic, social, societal and environmental innovation, with a view to improving overall performance.
In 2017, CEPOVETT Group's CSR policy was also reflected in the deployment of its responsible purchasing charter. This charter secures and assesses the best practices of each supplier. Its ambition is to help each production workshop improve its CSR practices. The Ukrainian textile company Siluet is an example of the successful integration of disability into a professional textile environment.
Focus 2017
2017 Report
CEPOVETT Group relies on an ambitious program to support its suppliers. The CEPOVETT Group "FabLab" program is based on a voluntary, collaborative approach with its garment workshops in its main production zones around the world (Eastern Europe, Asia and North Africa). Through experimentation and a multi-year 360° CSR action plan, it aims to bring out best practices in technical, economic, social, societal and environmental innovation, in the service of overall performance. In 2016, the CEPOVETT Group FabLab program involved technical cooperation, the pooling of know-how and co-construction between French industrial partners to demonstrate the industrial feasibility of a closed-loop garment concept derived from recycled clothing. It took almost 16 months of thought and research to bring to market a product made from 100% recycled fibers, in particular from customers' own post-consumer textiles, whose approach is fully in line with the circular economy. This first experiment is the logical extension of the CEPOVETT Group recycling program initiated in 2011. A further step towards eco-responsible professional clothing.
Focus 2016
"CEPOVETT Group Fablab", a lever for innovation excellence "CEPOVETT Group Fablab", a lever for innovation excellence
Beyond the aspects of audits and controls, CEPOVETT Group believes in supporting its garment factories over the long term, through the exchange of best practices, the transmission of know-how and co-production as a cooperative working model. Launched in 2014, the innovative "CEPOVETT Group FabLab" approach is an ambitious and exclusive program to support its industrial sites with the aim of turning them into genuine eco-socio-responsible showcases. In 2015, numerous best practices were tested on the industrial site. For example, a major effort to reduce environmental impact was made at the EPSILON industrial site in Madagascar, thanks to the implementation of a heat recovery process, produced by the business, as well as the use of biomass energy. With regard to the well-being of employees, sports activities (Zumba) have been organized and a canteen is available. Projects of general interest have also been organized with local stakeholders.